What is Porosity in Welding: Finest Practices for Preventing Permeable Welds
What is Porosity in Welding: Finest Practices for Preventing Permeable Welds
Blog Article
The Science Behind Porosity: A Comprehensive Guide for Welders and Fabricators
Comprehending the complex devices behind porosity in welding is vital for welders and producers making every effort for impeccable craftsmanship. From the structure of the base products to the complexities of the welding procedure itself, a multitude of variables conspire to either intensify or relieve the visibility of porosity.
Understanding Porosity in Welding
FIRST SENTENCE:
Assessment of porosity in welding reveals critical insights into the stability and high quality of the weld joint. Porosity, identified by the presence of tooth cavities or gaps within the weld steel, is an usual concern in welding procedures. These spaces, if not effectively resolved, can endanger the architectural stability and mechanical residential or commercial properties of the weld, leading to possible failings in the completed product.

To identify and evaluate porosity, non-destructive screening methods such as ultrasonic screening or X-ray inspection are often used. These strategies enable the identification of inner flaws without compromising the honesty of the weld. By analyzing the dimension, form, and circulation of porosity within a weld, welders can make enlightened decisions to boost their welding processes and accomplish sounder weld joints.
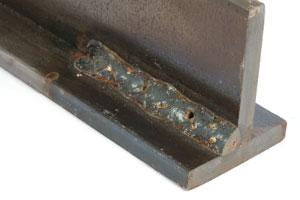
Factors Affecting Porosity Development
The occurrence of porosity in welding is affected by a myriad of elements, ranging from gas shielding effectiveness to the complexities of welding criterion settings. One essential variable contributing to porosity development is insufficient gas protecting. When the shielding gas, generally argon or carbon dioxide, is not properly covering the weld pool, climatic gases like oxygen and nitrogen can pollute the liquified steel, leading to porosity. Additionally, the tidiness of the base materials plays a substantial duty. Pollutants such as rust, oil, or dampness can vaporize throughout welding, creating gas pockets within the weld. Welding criteria, including voltage, current, take a trip rate, and electrode type, also effect porosity formation. Utilizing improper setups can generate extreme spatter or warmth input, which consequently can cause porosity. The welding technique employed, such as gas metal arc welding (GMAW) or shielded metal arc welding (SMAW), can influence porosity development due to variations in warmth distribution and gas coverage. Comprehending and controlling these aspects are important for minimizing porosity in welding operations.
Results of Porosity on Weld Top Quality
The visibility of porosity additionally deteriorates the weld's resistance to corrosion, as the entraped air or gases within the spaces can react with the surrounding setting, leading to destruction over time. Furthermore, porosity can hinder the weld's capability to endure stress or effect, further threatening the general quality and integrity of the welded framework. In vital applications such as aerospace, automotive, or structural constructions, where safety and security and sturdiness are paramount, the harmful results of porosity on weld high quality can have severe repercussions, emphasizing the value of minimizing porosity with correct check my site welding strategies and procedures.
Strategies to Minimize Porosity
To improve the top quality of bonded joints and guarantee architectural honesty, welders and fabricators utilize particular strategies focused on lowering the formation of voids and tooth cavities within the product throughout the welding process. One effective approach to reduce porosity is to make sure correct material preparation. This includes detailed cleaning of the base metal to get rid of any pollutants such as oil, grease, or wetness that might add to porosity development. In addition, making use of the proper welding parameters, such as the proper voltage, existing, and travel rate, try here is critical in avoiding porosity. Preserving a regular arc size and angle throughout welding also helps in reducing the likelihood of porosity.

Making use of the suitable welding strategy, such as back-stepping or utilizing a weaving activity, can likewise help disperse heat equally and minimize the opportunities of porosity formation. By applying these techniques, welders can properly reduce porosity and generate premium bonded joints.
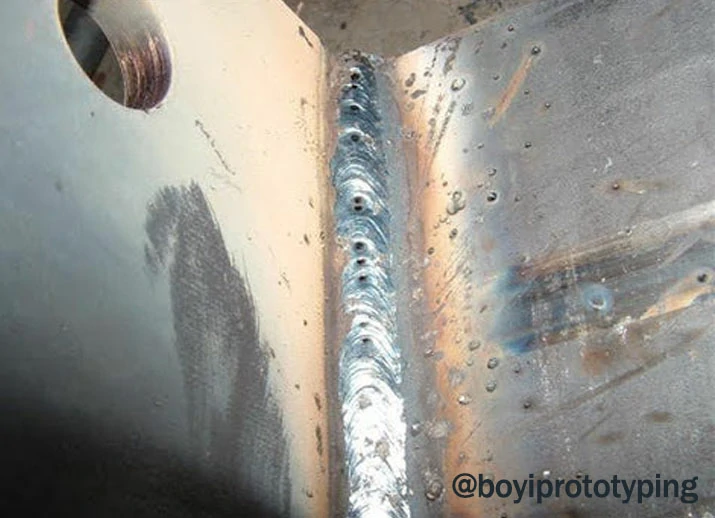
Advanced Solutions for Porosity Control
Implementing innovative modern technologies and ingenious approaches plays a critical duty in attaining superior control over porosity in welding processes. Furthermore, utilizing innovative welding techniques such as pulsed MIG welding or changed ambience welding can additionally help minimize porosity issues.
An additional advanced service involves the usage of advanced welding devices. As an example, using devices with built-in functions like waveform control and sophisticated power resources can improve weld quality and lower porosity risks. The implementation of automated welding systems with precise control over criteria can dramatically lessen porosity flaws.
Additionally, including innovative monitoring and inspection innovations such as real-time X-ray imaging or automated ultrasonic screening can aid in detecting porosity early in the welding procedure, permitting immediate corrective activities. Overall, incorporating these sophisticated solutions can substantially improve porosity control and improve the total high quality of welded parts.
Conclusion
Finally, understanding the scientific research behind porosity in welding is essential for welders and producers to generate top notch welds. By identifying the variables influencing porosity development and executing strategies to decrease it, welders can boost the general weld top quality. Advanced services for porosity control can additionally enhance the welding process and make certain a solid and dependable weld. click for info It is very important for welders to continuously inform themselves on porosity and implement finest methods to attain optimal outcomes.
Report this page